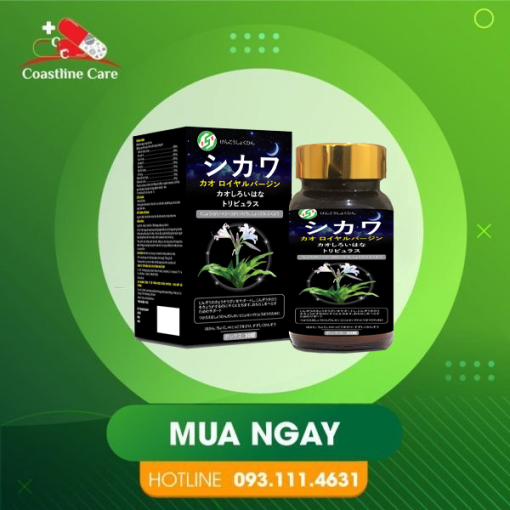
One more challenge is making sure that duties or adhere to-ups are assigned to the right individual or crew. In a remote setup, it’s easy to ignore who’s to blame for what and to trace jobs that aren’t assigned right away. Nonetheless, you'll find instruments like SafetyCulture (formerly iAuditor) which can help using this concern.
Its simplicity, nevertheless, can even be its greatest downside as it doesn't always expose the scale or significance of Anybody issue, which makes it tougher to prioritize motion.
Consequently smaller challenges can be supplied additional consideration than they need to have and huge ones not enough. Because A great deal with the diagram's inputs and interpretations are subjective, it might also cause disagreements amid managers who check out the chart from various perspectives.
Immediately after graduating, Ishikawa in the beginning served during the Japanese Navy to be a technological officer. His tasks bundled engaged on chemical weapons and gas creation, roles that honed his capabilities in systematic Examination and approach Regulate.
It's also possible to utilize the scientific approach in the form with the nicely-acknowledged plan-do-Examine-act (PDCA) cycle to empirically look into the failure. Often, failure investigations begin with brainstorming attainable results in and listing them in an Ishikawa diagram. This isn't automatically Completely wrong, but frequently the Strategies listed usually do not lead to your failure less than investigation.
Root-cause Investigation is intended to expose crucial relationships between a variety of nha thuoc tay variables, along with the attainable will cause supply extra insight into method behavior. It displays large-degree triggers that bring about the challenge encountered by delivering a snapshot of the present scenario.[1]
The Ishikawa Diagram stays a elementary Resource in quality Manage, and top quality circles keep on being a important practice in many companies.
Device – This refers to the assets which include equipment and devices utilised to generate or supply the service or product.
Good quality circles usually encompass a little team of employees from the similar operate region who meet up with frequently to detect, assess, and fix work-linked challenges. The process involves:
Each result in or basis nha thuoc tay for imperfection is often a supply of variation. Leads to are frequently grouped into important categories to determine and classify these sources of variation.
Examine the Diagram: Critique the diagram to identify relationships and prioritize brings about for even further investigation. You can prioritize utilizing real info, multivoting, nominal group strategies, or getting consensus within the team.
Produce the condition assertion at the center-correct from the flipchart or whiteboard, box it, and draw a horizontal arrow running to it.
Every single of these groups branches out additional to record prospective causes relevant to Every single category. This Visible tool can help teams systematically Imagine from the root triggers of a difficulty, rendering it simpler to identify alternatives.
By involving employees in any way degrees, Ishikawa’s approaches encourage a lifestyle of constant enhancement that is certainly essential for organizational good Shikawa results.